The Theta Project was launched in 2019 for the company Beneš & Lát, which utilizes high-pressure aluminum injection molding technology at its plant in Mimoň. The project’s original goal was to develop a system for continuous monitoring of physical variables during the production process. However, the measurement system developed has proven valuable for tasks related to the use of conformal cooling and variable structure cooling in casting molds, where it enables precise monitoring of production parameters.
Technical Specifications
In casting molds, oil is typically used as the tempering medium, while water is used in the cooling circuits. Oil circuits reach temperatures above 200 °C, while cooling circuits have a maximum temperature around 90-100 °C. The device is engineered to accommodate these ranges. ThetaBox allows for the monitoring of temperatures, flow rates, and pressures within individual circuits, enabling detailed diagnostics of the entire process and identification of potential production deviations. This allows for the stabilization and optimization of the production cycle, capturing abnormal conditions to provide operators with early warnings.
The operating ranges of the measured variables are as follows:
- Temperatures: 0-700 °C
- Pressures: 0-12 MPa
- Flow rates: 11.3-113 LPM (high-temperature circuit); 2-40 LPM (low-temperature circuit)
The measurement system enables data storage in the device’s local storage and transmits data over WiFi to the network using the MQTT protocol. Measurement frequency and other parameters can be defined by the user through a simple configuration file stored in the device’s internal memory. By default, measurements are recorded every second.
Key Enhancements
- Integration of an SD card reader for data storage.
- A WiFi module enabling online data transmission to the company’s system.
- Introduction of a ‘beacon’ mode, which automatically activates warning devices, such as machine warning lights, when set limits are exceeded.
“The Theta Project is an important step for us in implementing modern technologies in industrial production. Thanks to ThetaBox, we are reducing production defects, increasing production quality and speed, and reducing the energy consumption of the production process,” says Ing. Tomáš Jetmar, General Manager of NCK MATCA.
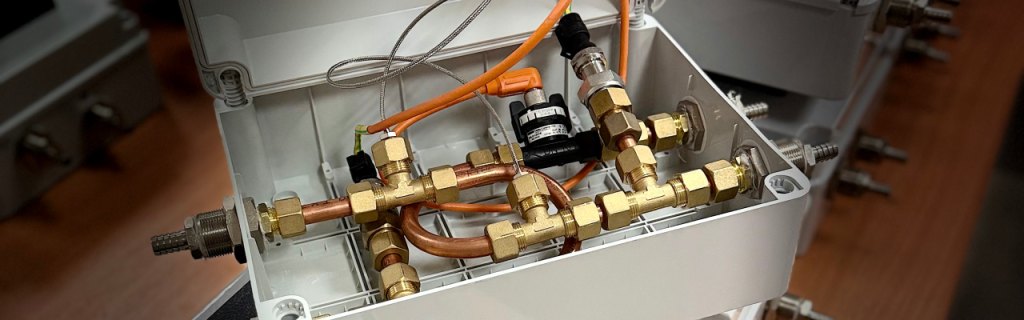
Beneš & Lát: https://www.benesalat.cz/